Blog
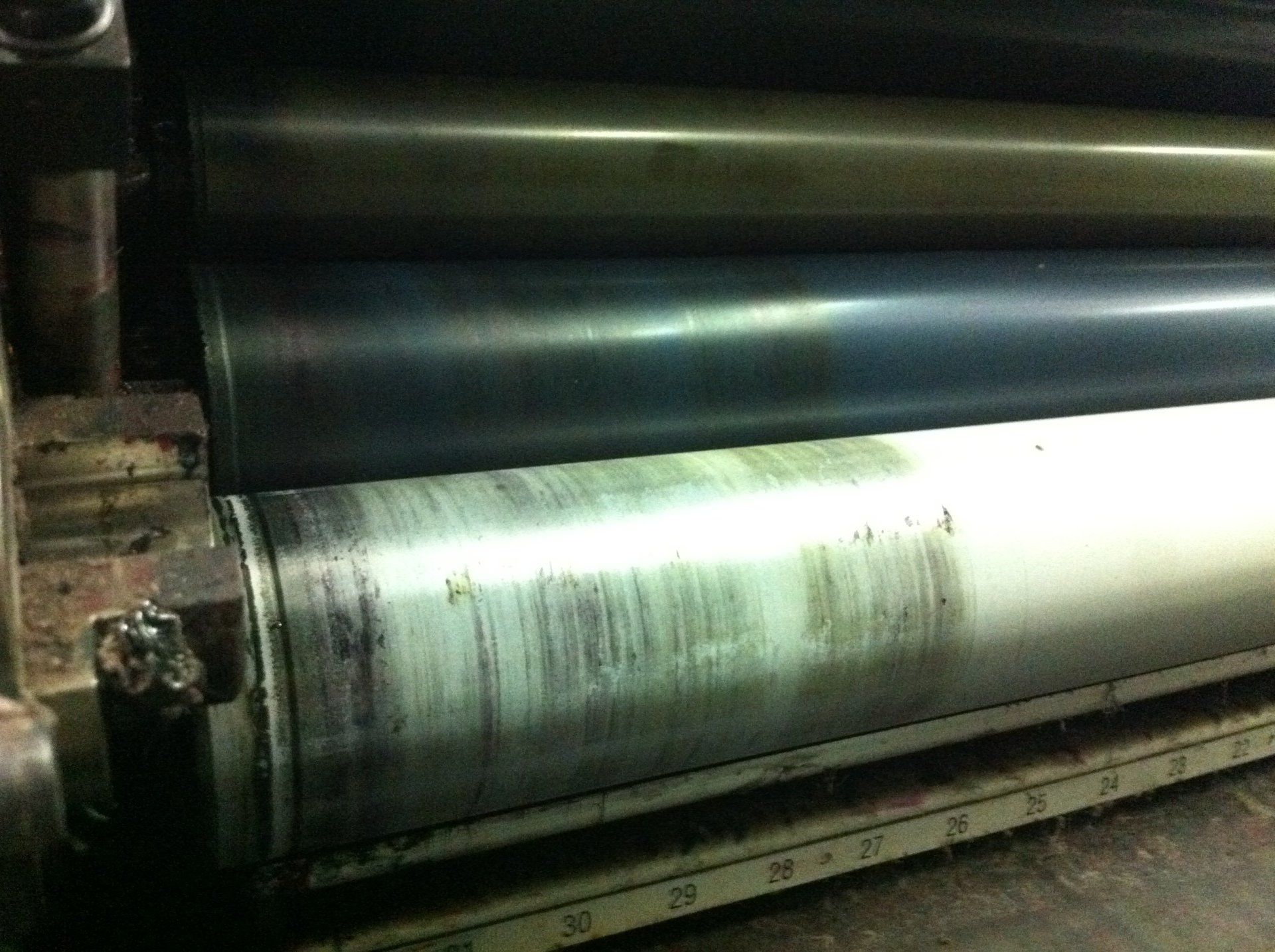
Right at the beginning I would like to link the pictures here on top! You are welcome to leave your opinion about them in the comment field. I think that with these dampening systems no proper printing is possible anymore, but in offset printing the dampening system is an important factor for stable and good results or print products. Due to my worldwide activities at printing machines it can be seen that not always production printing and therefore missing maintenance intervals or cleaning work lead to problems in the dampening system. Again and again it comes through: incorrectly adjusted rollers, heavily worn rollers, Wrong roll cover / rubber, incoming chrome distributors, wrong additions, bad IPA or IPA replacement, to dirty fountain solution, the wrong cleaning products, leakage in pneumatic cylinders, to problems up to unwanted machine downtimes. The problems often show up in toning, smearing, emulsification of the ink, lack of color brilliance, color fluctuations, framing, etc. I don't want to go into detail now, but it must be mentioned that fountain solution plays a major role in a well-functioning dampening system. Especially the parameters additives, roller material and print product should be coordinated with each other, i.e. with which raw water quality, which roller material and which print product (labels, packaging etc.) you start with. These are only some of the basics to be considered. You can read more basics in my book "Printing Inside". Often badly adjusted rollers are a reason for the problems. So the adjustment to the plate can be checked quickly, also the pan-roller and chrome-distributor-roller usually make a good impression. Since it is directly in the viewing area. But many operators shy away from removing the chrome- distributor-roller (Dicke Berta) and checking the adjustments of the other rollers, or out of ignorance. The time required for this is rather short if used regularly. Tap forwards / backwards a few times and an assessment of the parallelism and thickness of the contact strips is done. Even small adjustments are possible. When times come, the dampening unit should then be completely removed and the roller surface and diameter checked. Of course the rollers can also be replaced. In this breath, cleaning of permanently installed rollers is a good idea. If you are unsure about how to adjust the dampening units, you can refer to the operating instructions or get help from instructors. Aids such as a strip card or even a NIPCON for assessing the contact strip thickness would be advantageous. A moisture test form such as the one from Fogra will help to find the optimum setting. It is also important which washing agent you use to clean the dampening unit or dampening rollers. Not all washing agents are suitable or approved for the roller material in the damping unit. Defective surfaces in the material and/or impurities in the dampening water can quickly occur. If you are not sure whether and which washing agent is suitable for your dampening rollers, you can ask the manufacturer or supplier. Conclusion: By checking the adjustments and visual assessment of the roller surfaces, problems can be prevented. It is also advisable to control the process water and to coordinate it with the printing and press portfolio. A more stable and qualitative production can be achieved by regularly applying the controls. Comments and feedback are welcome. I now wish everyone a good time and much success. Your Uwe Schulczek